Interest in electric vehicles (EVs) has skyrocketed due to their perceived role as the future of transportation. EVs offer increased energy efficiency and emit fewer pollutants. From a manufacturing standpoint, electric cars are simpler and contain fewer components compared to gas-powered vehicles. However, Thailand heavily relies on fossil fuels to generate its electricity with over 70% of its electricity generated from natural gas. This raises the question of whether there are alternative vehicle options that are more environmentally friendly than EVs in the Thai context.
Indeed, there are alternative options available, such as hydrogen-powered cars, which are widely regarded as the cleanest and most environmentally friendly vehicles in the world. Hydrogen, the most abundant element on Earth, reacts electrochemically with oxygen from the air, producing only electricity and water without any harmful emissions. This unique characteristic has led to the development and commercialization of numerous hydrogen-powered electricity generators in recent decades, supported by advancements in hydrogen production technologies.
Thailand holds a prominent position as the leading global producer of energy crops like sugarcane and cassava. Annually, the country produces over 6 million liters of ethanol, which is used for blending with gasoline as engine fuel. This vast quantity of ethanol serves as a substantial source for hydrogen production. The conversion of ethanol into hydrogen not only provides clean energy but also adds value to farm commodities.
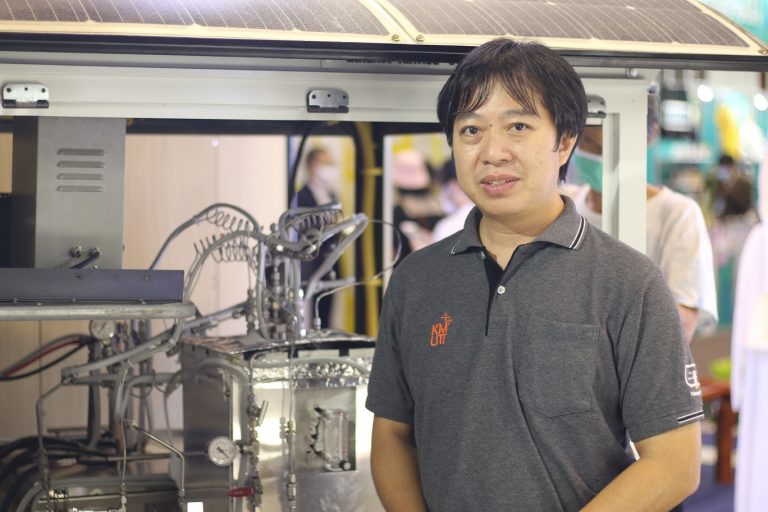
Assist. Prof. Dr. Nutthapon Wongyao from the KMUTT Pilot Plant Development and Training Institute (PDTI) spearheaded a project funded by the Electricity Generating Authority of Thailand (EGAT) to develop a portable fuel production system using ethanol. The primary objective of the project was to create an ethanol-to-hydrogen conversion process.
Dr. Nutthapon explains that his team has successfully designed a hydrogen production system through the steam reforming of ethanol, utilizing nickel as a catalyst. This process generates syngas, which contains over 90% hydrogen. The compact and portable reactor developed by the team is easy to install. It is then connected to a solid oxide fuel cell (SOFC), an electrochemical conversion device that generates electricity directly from the oxidation of hydrogen gas. The SOFC can also utilize methane gas and carbon monoxide to produce electricity. To test the ethanol-based electricity generation system, it was implemented on an electric 3-wheeler (Tuk Tuk) equipped with a 1 HP electric motor. The generator successfully powered the Tuk Tuk at a speed of 20 km/hr. The 1 kW hydrogen production system consumes 0.23 liters of ethanol per hour and has an estimated cost of THB 70,000.
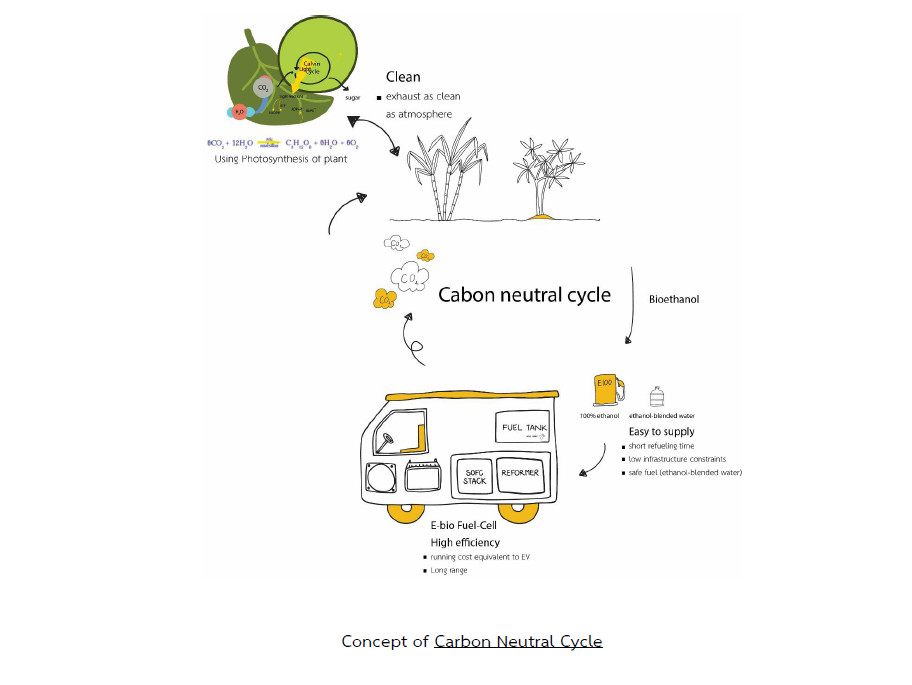
Further research and development are necessary to incorporate the ethanol-to-hydrogen conversion technology to hydrogen cars. “To drive research and application of hydrogen cars in Thailand, the government needs to provide a clear policy and support measures similar to those for EVs,” emphasizes Dr. Nutthapon. He also recognizes the potential of this technology to supply electricity in remote and isolated areas lacking access to power, as well as in disaster zones.
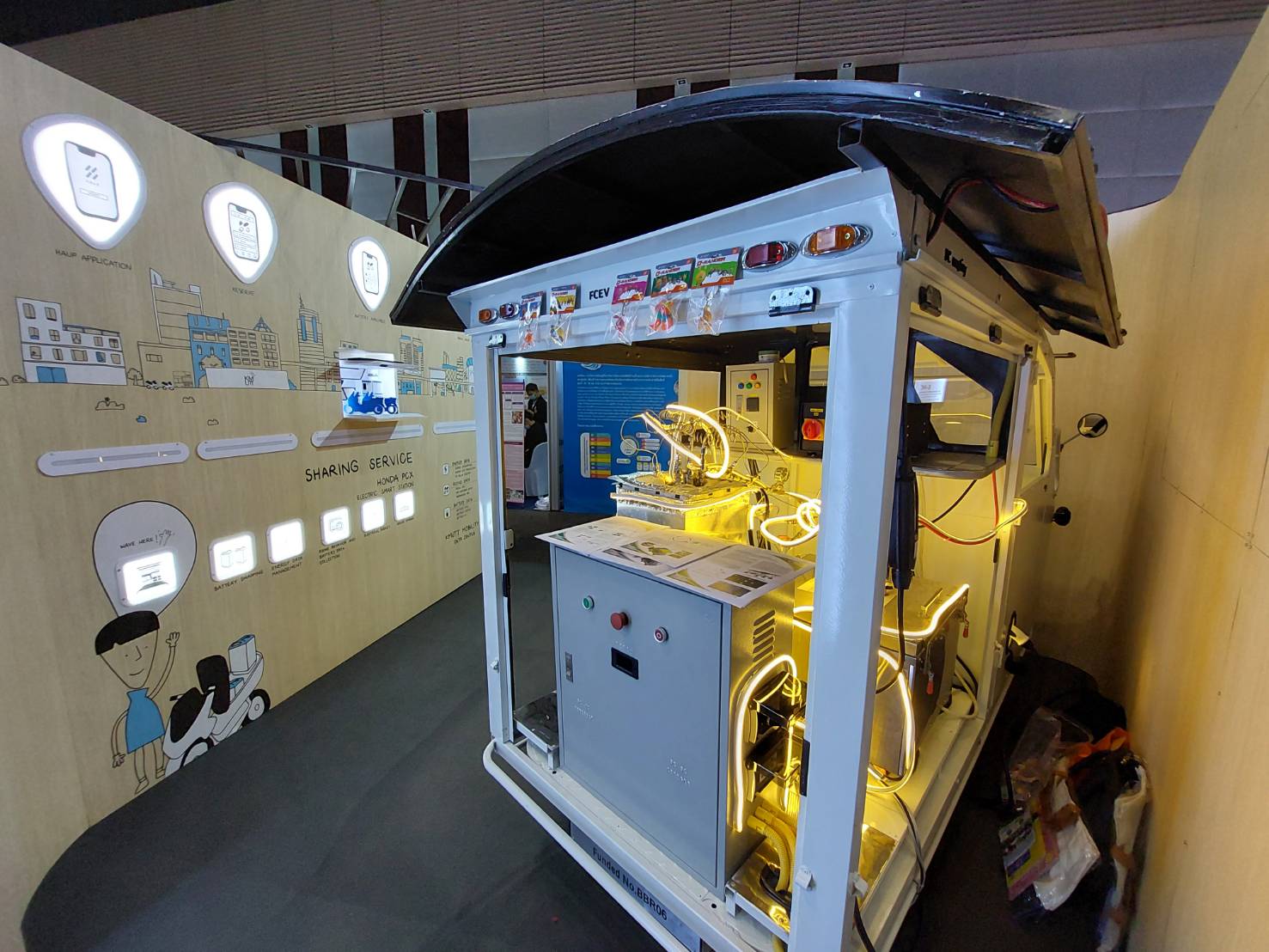
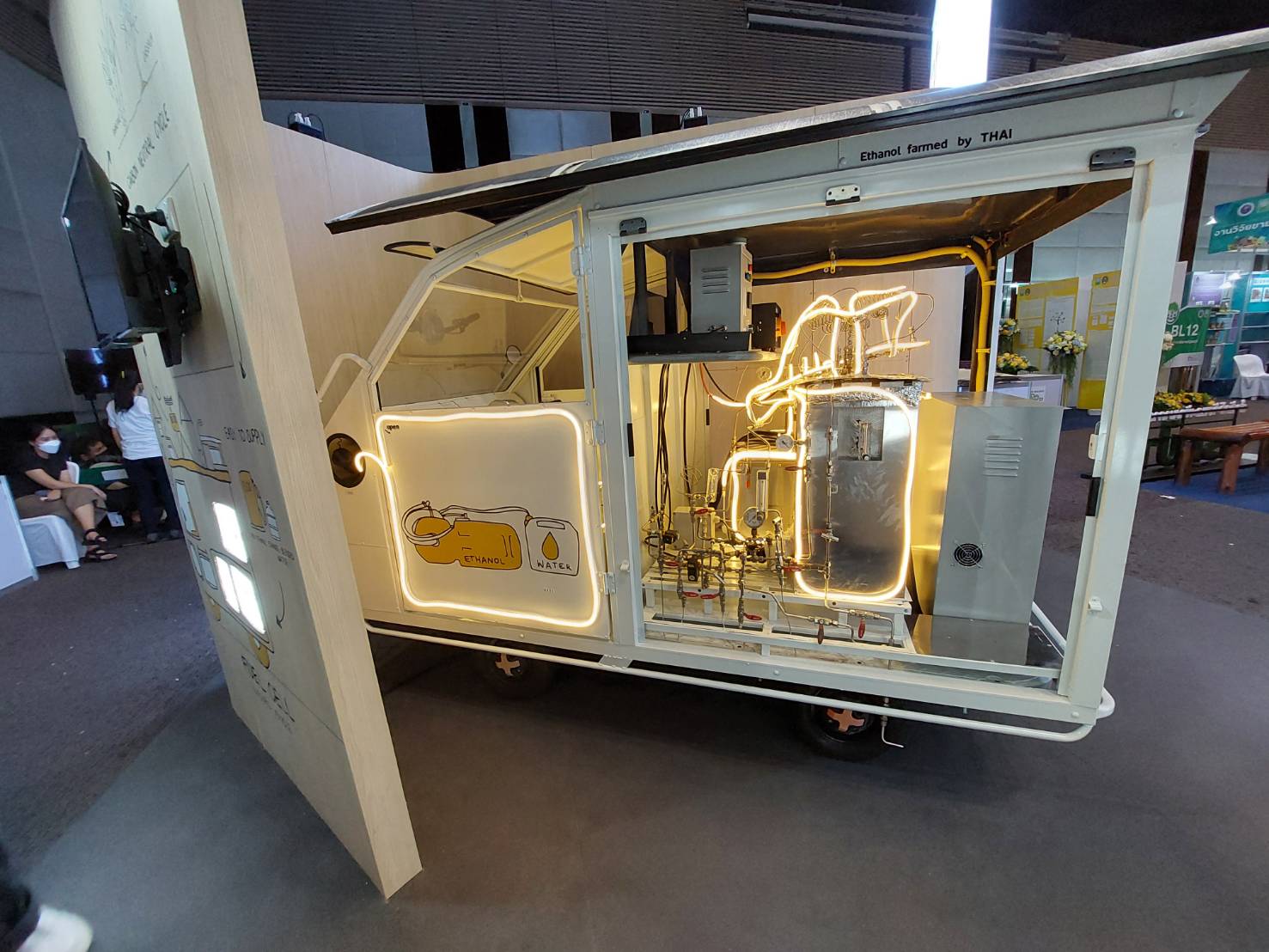
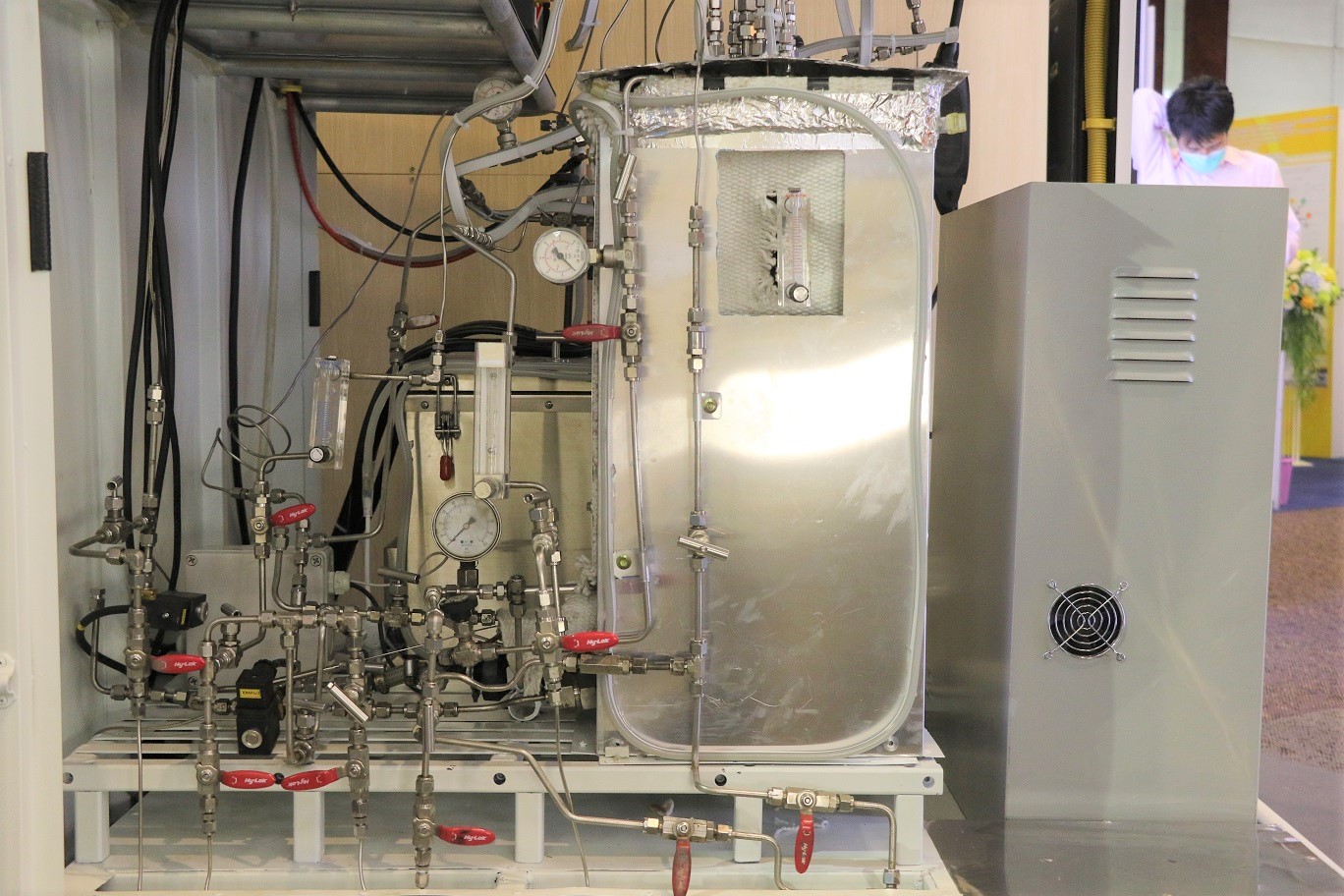
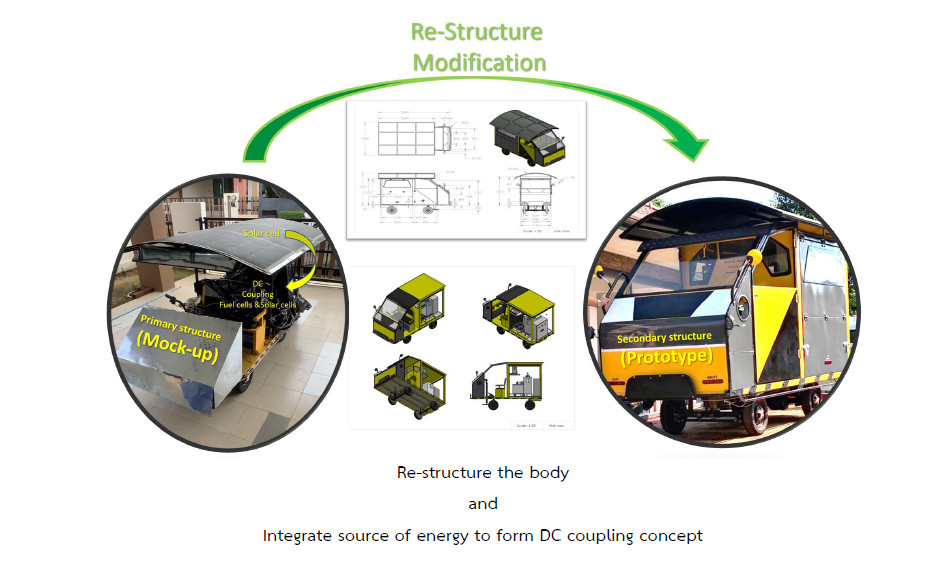
Dr. Nutthapon explains, “By integrating multiple sets of the hydrogen production system, the capacity for electricity generation can be multiplied, allowing for the establishment of hydrogen-based power plants serving larger communities or functioning as EV charging stations. Unlike solar power plants that rely on sunlight, hydrogen-based power plants offer the advantage of producing electricity consistently throughout the day and night. Additionally, apart from ethanol, this hydrogen production system can utilize other raw materials such as biogas containing methane.”
For the next phase, Dr. Nutthapon plans to combine the hydrogen production system and the electricity generation system into a single unit, reducing complexity and the number of parts and components. This integrated unit will find broader applications in various industries.
This research project undeniably benefits various sectors of society, including sugarcane and cassava farmers, as well as small- and large-scale ethanol producers. Moreover, the innovation contributes to energy security and supports climate action.
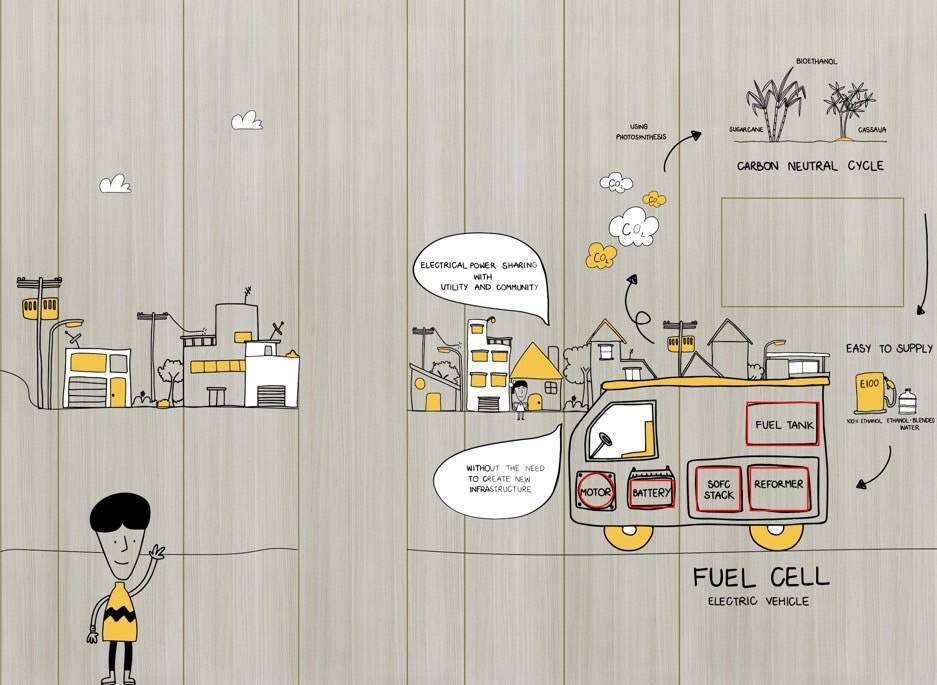